- 热点文章
-
- 09-14关于高等职业院校弱电专业教改的探索
- 11-28东芝将在2009年CES带来新水平的前沿技术
- 11-28互联网:世界的镜子
- 11-28中美文化论坛研讨数字技术保护文化
- 11-28浅析“三鹿集团奶粉事件”危机根源
- 11-28新媒体的发展及其教育创新应用研究
- 11-28楼宇信息系统的现状与应用以及发展趋势
- 11-28中国2009世界邮展60城市巡邮漯河站启动
- 11-28打造焕发生命活力的教育时空
- 11-28观察中国管理教育30年
- 11-28驾驭论:科学发展的新智囊
- 11-28软着陆将解读中国管理国际化新走势
- 11-28创建中国水电国际化强势品牌
- 11-28管理科学进入新观察时代
- 11-28全球化传播语境下的家国建构
- 11-28网络民主对公民社会建设的影响研究
- 11-28奥运后中国酒店业的发展分析
- 11-28国家创新系统下的大学科研管理研究
- 11-28高校数字图书馆建设及服务模式探讨
- 11-28非均衡理论及我国房地产市场供求
- 11-28绿色、安全和通讯是汽车电子的未来
- 11-28敦煌莫高窟将为游客建"数字洞窟"
- 11-28思科新软件平台帮媒体公司建社交网络
- 11-28苹果乔布斯:用13年给IT业洗一次脑
- 11-28海外传真:2008年数字印刷市场回顾
- 11-28东芝将在2009年CES带来新水平的前沿技术
- 11-28互联网:世界的镜子
- 11-28中美文化论坛研讨数字技术保护文化
- 11-28故宫国图面临“数字化”难题 缺乏专门人才
烷基化硫酸反应器密封设计分析与计算
2023-08-28 13:38:00 来源:优秀文章
摘 要 :烷基化装置主要以较为成熟的硫酸法为主,DuPont(杜邦)公司的 Stratco 工艺是目前全球对烷基化油生产的主要代表 性工艺,Stratco 卧式偏心反应器是当今最为成熟的搅拌混合反应器且市场占有率极高。因此对国内市场而言,机械密封的可靠性是其 能否长期平稳运行的重要保障。通过结构布置及理论计算,深入分析硫酸反应器密封的设计要点,主要从两个方面进行理论分析。 一 是结合工艺流程,从传热机制角度确定选型方案 ;二是通过控制端面间界面形状改善机封的运行状态,合理利用以往成功的技术理念 给出结构参数,利用有限元软件进行分析校核,输入实际工况参数后结合流、固、热耦合迭代,计算出较为可靠的理论结果,最后通 过模拟试验对比验证结构参数的可靠性。
关键词 :烷基化装置 ;机械密封 ;传热机制 ;结构参数
中图分类号 :TE96 文献标识码 :B 文章编号 :1671-2064(2023)10-0076-07
1 选型及方案
1.1 密封设计难点
1.1.1 工艺复杂
Stratco 卧式烷基化反应器是一种液压混合机,专门 用于酸性催化剂对烃类进行烷基化,同时去除烃类化学反应产生的热量,复杂的工艺流程对机封的长周期运行有很大挑战。对机封来说,其强腐蚀性、黏度大等特性, 目前技术手段处理已非难事,通过材质升级便可满足应用,但机封面对其复杂的工艺流程,对稳定、长周期的运行有着很大的挑战。
1.1.2 工况苛刻
(1)轴摆及振动。接触器内流体的循环受到位于液压 头特殊轴流式叶轮的影响,物料在抽送过程中,与轴相连的叶轮会遭受流体强力剪切作用及高度湍流冲击作用(见图1),因此轴摆及振动对机封运行的稳定性是有极大影响的。
图1 设备示意图
(2)外冲洗选择。部分终端在使用过程中机封并无外冲洗,这将大大影响机封使用效果,某炼化厂烷基化装置 三机一开两备情况下连续生产一年都极为困难。而烷基化反应器的工艺流程为 :低温时在硫酸催化剂的作用下,碳四进料中的烯烃与异丁烷发生烷基化反应,生成以带支链异辛烷为主的反应混合物 ( 即烷基化油)。根据工艺需求,此机封采用的外冲洗流体为参与反应原料之一,即碳四。
(3)密封腔内操作条件稳定性。此工艺流程中,脱去游离水后的碳四与闪蒸罐来的循环冷剂混合后进入反应器,一般而言,其 Plan32 冲洗流体工况范围是 0.5 ~ 0.8MPa、 7 ~ 9℃。一方面从传热机制角度讲,此时碳四在该操作 压力下呈现液态,但其饱和蒸汽压随温度的升高会急剧增大,易发生汽化现象,因此机封环体对外冲洗流体的对流传热必须严格控制 ;另一方面从蒸汽压力角度讲,需保证前置缓冲套起到节流保压作用,避免早期磨损使密封腔内冲洗流体(液态碳四)直接汽化,同时控制间隙内的一定流速使少量反应生成的胶状物隔离在缓冲套另一侧(见图2)。因此其核心点在于保持密封腔内冲洗流体在一定温升范围内不会产生汽化问题,以达到减小冲洗流量的目的, 避免稀释工艺流体。
图2 缓冲套示意图
1.2 密封与系统方案
针对以上工况及生产工艺需求,制定如下方案(见图 3)。
1.2.1 密封方案
布置方式 3,3CW-FB A 型密封。
1.2.2 系统方案
Plan 32+53A ,隔离液为耐酸型航空液压油。
1.2.3主要材料选择
介质侧端面采用碳化硅配对碳化硅,大气侧端面采用石墨配对碳化硅 ;金属材料采用耐蚀合金 NS1403 ;弹簧采用哈氏合金 NS3303 ;辅助O形圈采用全氟醚橡胶。
2 结构特点分析
2.1 内置轴承
轴承采用调心滚子轴承,能够补偿一定的同轴度误差,也可实现自动调心,避免与设备发生轴系干涉或过定位问题,同时具有较好的抗冲击能力及较强的承载能力。 不同于以往搅拌器机封轴承的安装位置,此机封将轴承安装在两组端面之间,可以提高机封抗摆能力,提高轴系的刚性,改善桨叶强烈的振摆情况,还可以避免远端缓冲套被动承担支点的作用,降低缓冲套间隙处的磨损程度,使其功能性寿命大大延长,这对密封腔的保压及阻隔效果有明显提高。
但内置轴承也有其短板,需严密考虑。其本身在转动 过程中会产生一定摩擦热,虽然这些温升对轴承本身并无影响,但对于机封则显得尤为关键。
2.2 串联布置
此工况的常规选型一般是 3CW-BB(双端面 - 背对背 布置),但对于内置轴承的产热问题并无法很好解决。大气侧密封与轴承等旋转件的产热基本由系统的换热单元承担,从对流传热角度分析,介质侧密封的温升若无法有效控制,则环体附件的液态碳四则会发生汽化或沸腾,在气 泡溃破过程中产生的水力冲击是机封无法承受的,尤其对于碳化硅端面的机封。一方面是端面液膜失稳,流体承载 与接触承载比例失衡,使得端面出现严重刚性接触并发生过度磨损,对于硬对硬材质的摩擦副端面是不可逆的损坏,极易造成热弹失稳引发严重后果 ;另一方面是滑动O形圈发生频繁“章动”使滑移直径处磨损加剧,易发生早 期失效,甚至在O圈压缩比过大时,弹簧无法提供足够的补偿克服阻尼,在频繁的水力冲击中发生端面崩牙,造成环体破裂。
因此在考虑传热效应的情况下,机封采用串联布置。对于介质侧密封而言,Plan32 冲洗存在强制对流现象,因此根据牛顿冷却定律 Q=αA(T-Tw) 可知,增加环体的对流换热面积并充分利用低温碳四的冲洗效果,可以有效达到降温的目的 ;在密封腔内,由于转速较低,旋转件引起的黏滞阻力在冲洗流换热的情况下,所产生的热量并不会对介质侧密封所处的密封腔环境造成影响,因此端面接触摩擦产生的热量为密封腔内的主要热源。对于大气侧密封而言,需保证其在高压差下运行时,端面间的界面形状保持趋近平行间隙而不会产生严重畸变。大气侧密封由于承受更高的压差,在流体力作用下,截面形状受力弯曲产生的力变形更加明显,因此需通过有限元分析优化结构参数,让其由温度产生的热变形可以足够补偿压力导致的力变形,使得端面在耦合后的平行间隙下稳定运行,避免在油类这种高黏流体中因界面畸变产生强烈的流体动、静压效应,密封端面承载能力过大导致开启或流体承载力过小,使端面刚性接触而发生严重磨损。
另外需注意,由于工艺波动、报警失效等不可抗拒因素的存在,介质侧密封需考虑反压操作情况,大气侧密封需考虑介质侧密封完全失效时承担主密封的情况,这些将在设计计算模块继续论证。
2.3 导流套
一方面通过导流套剪切流体产生强烈湍流效应,有利于对流传热,避免在环体表面形成层流底层,因传热热阻的存在造成较大温差。而在 Plan32 外冲洗与套体剪切的共同作用下,由于流体质点剧烈混合,可近似地认为无传热热阻,即在 Plan32 的冲洗流体中基本上没有温差,如此避免了环体周围的碳四不会因温差发生汽化或沸腾,有利于机封运行的稳定性。
另一方面,在导流孔的离心引流作用下,避免反应残留的胶状物在组件缝隙内积聚,堵塞弹簧或使滑动O形圈挂起,增强局部空间内流体的流动性。同时由于采用小 弹簧外置及滑动O形圈暴露在工艺介质中,导流套可保护暴露在工艺介质中的各旋转零件,避免因遭受颗粒性物质的冲击而造成零件损坏情况的发生。
3 理论计算及模拟分析
3.1 理论计算
3.1.1 衡量标准
(1)端面温升 ;(2)承载比例 ;(3)摩擦(摩擦能耗、 生热,包括发生摩擦的位置) ;(4)磨损速率 ;(5)泄漏 率 ;(6)运行的一致性和稳定性。
3.1.2 参数标准
(1)端面材料 ;(2)平衡比 ;(3)端面宽度 ;(4)传 热环境 ;(5)力变形锥度 ;(6)热变形锥度。
3.1.3 计算步骤
首先对二级密封进行理论计算,大体确定结构参数后,进行有限元分析校核,根据模拟出的结果对密封进行有限元计算。大气侧密封参数计算如下 [1]。
此时密封面闭合,端面处于混合摩擦状态,利用混合 摩擦状态下密封端面的摩擦热计算公式计算得出 :
利用一端对流传热的肋片导热法,求出端面平均温度 [2]。
图4 摩擦副简化图
对于结构复杂的动环,根据截面形心位置简化动环为 L 形截面环(见图 4),使整个端面均匀热流,左环体计算 (环体材质浸锑石墨,流体为轻质油) :
根据流量需求,此工况下内置泵送环必须保证足够流量以满足降温要求,所产生压头可克服管阻即可。根据经验,此密封采用双向泵送,待试验模拟时实测流量是否满足要求。
另外,对于大气侧密封需充分考虑密封的承载能力。 机封需能够承受频繁轴摆及在介质侧密封完全失效的情况下承担主密封的作用,故在可控范围内,选择通过增加端 面宽度及加大平衡比,提高机封抗摆能力及承载能力。其中,在参数设定上需考虑因端面加宽引起温度梯度产生较大的径向锥度,由此造成的收敛型间隙,由于其较低的摩擦系数,虽然可以降低磨损,但泄漏量可能会有所增加, 并会在此状态下长期持续发生 [3]。若产生过大的径向锥度则会造成局部发生刚性接触,接触承载与流体承载比例失衡,在较大的接触力下造成过度磨损,或引起端面间膜压系数增加造成开启力过大,在摆动过程中发生喷漏的现象。因此,对于大气侧端面间隙的界面形状,希望其在运行状态下达到的是偏收敛的平行间隙(1 条氦光带以内), 在液相流体膜作用下,端面所受全部载荷在理想状态下基本由流体压力承担,使得密封面在全液相下轻微接触且只允许有限的摩擦生热及轻微磨损,通过计算使得端面的间隙最小,以此来控制泄漏量。
假设初始锥度与热锥度引起的净径向锥度为 1 条氦光 带,则 Φ=5.1×10-5
此模型为假定端面间界面形状呈收敛型间隙,其膜压系数升高及黏性流体剪切时端面间隙间产生的热流体动力楔效 应并未考虑,手工计算较为复杂,需借助有限元建模分析。
3.2 大气侧密封 FEM 有限元分析计算
基本参数在初步设定的基础上,结合以往设计经验, 重新精确给出参数,以此为基础利用有限元在传热边界、 压力边界、材料区域、等温线、温度引起的挠度、压力引起的挠度、总缺陷、应力分布和安全系数等方面进行校核及优化(见图 5)。
图5 模型网格划分
3.2.1 未磨损时端面计算结果
具体数值见图 6 和表 2。
表2 计算项目及结果

图6 摩擦副总变形量、摩擦副应力分布
3.2.2 稳态时端面计算结果
具体数值见图 7 和表 3。
(1)变形趋势 :密封端面从初始状态到工作稳态后, 运转工况下的端面变形量为+0.4条氦光带(1条氦光带约为 0.29μm),仅仅是微小的变形量,不会引起界面形状的畸变。由于高压差的存在,压力产生的变形还是较为明显的。因此需要设计为由压力引起的负径向锥角在温度导致的正径向锥角补偿后能够在近似平行的微收敛间隙下运行,此时流体膜为正刚度,端面承载能力大、液膜刚度稳定、抗摆动性能强,端面间以流体承载占主导地位,此时在开车、停车期间,不会发生严重磨损。此变形量在石墨环磨损后,摩擦副端面将呈近似平行间隙运转。(2)端面力分布 :经模拟计算,此时端面的总承载力F 总=2063N,接触力 Fc=243N,接触力占比仅为 11.77%, 由剪切引起的热流体动压效应产生的开启力占比 25.25%。因黏性剪切引起的功率消耗比为 91.2%,因接触摩擦引起的功率消耗比为 8.8%。存在接触力并不意味着一定会发生过度磨损,收敛间隙会在一定程度上降低磨损系数,使密封保持在低磨损、低泄漏量的状态下持续运行至平行稳定状态,不至于在全液相非接触状态下发生喷漏等情况。
3.3 介质侧密封 FEM 有限元分析计算
3.3.1 未磨损时端面计算结果
从图 8 和表 4 可以看出,未磨损时端面应力分布、热锥度以及模压,有如下特征。
图8 摩擦副总变形量、摩擦副应力分布
(1)变形趋势 :密封端面从初始状态到工作稳态后, 运转工况下的端面变形量为+0.3条氦光带(1条氦光带约为 0.29μm),仅仅是微小的变形量,不会引起界面形状的畸变。碳化硅环由于其自身机械性能的高抗可压性,其向内外的弯曲趋势不明显,因此在此模型中重点考虑温度梯度引起的热变形影响。此时的端面变形几乎全部是由温度变形所导致的,而在实际操作条件下,介质侧环体周围的传热机制为环体对 PLan32 冲洗流体进行对流传热、 环体本身为热传导、环体对 PLan53A 隔离流进行对流传热,通过将 PLan32 冲洗孔靠近机封端面, 同时导流套辅助形成湍流,在零件转速及冲洗流速较快的端面附近可有效提高对流传热系数,因此在实际运行过程中温度梯度引起的热锥角可能要更小,端面的界面形状更趋于平行状态。
(2)端面力分布 :经模拟计算,此时端面的总承载力F总 =2371N,净受力为F净 =538N,接触力Fc=20.5N接触力占比仅为 3.8%。因黏性剪切引起的功率消耗比为99.7%,因接触摩擦引起的功率消耗比为 0.3%。考虑到硬对硬密封磨损后的不可逆性,尤其在开车、停车时短暂地发生半干摩擦或干摩擦,这将严重影响间隙的界面形状及后续的运行状态。对于此模型,由于端面间接触力极低,基本可看作为始终保持非接触状态运行。
(3)环体温度梯度 :从分析模型中可以看出,整个环体的温度稳步较为均匀,并无温升梯度过于积聚的情况, 这对于密封腔操作环境的稳定性有着极大提高,不会引起端面附近的介质发生严重相变,这也符合设计初衷。让端面始终在全液相流体膜作用下稳定运行,端面所受全部载荷在理想状态下基本全部由流体压力承担,使得密封面在全液相下仅有极小的轻微接触且只允许有限的摩擦生热及粗糙度级别的轻微磨损。
表4 计算项目及结果
3.3.2 极端工况计算结果
从图 9 和表 5 看出,极端工况下端面变形、流膜状态以及膜厚分布,具有如下规律性特点。
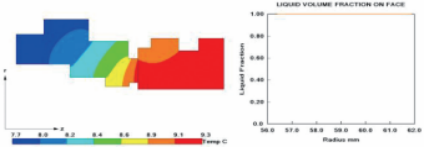
图9 摩擦副总变形量、端面液体体积分数
表5 计算项目及结果
(1)变形趋势 :此模型模拟为 Plan53A 压力不足, 介质侧密封出现反压时的运行状态,此状态下端面几乎成平行间隙运行,不会因界面形状的畸变而发生严重磨损。碳化硅环由于其自身机械性能的高抗可压性,其向内的弯曲的趋势不明显,因此在此模型中重点考虑端面间的流体膜状态。反压状态下,端面间的流体膜由油膜变为轻烃膜,前期设计的反压平衡比较高,因此不会发生喷漏现象。此时需考虑端面间是否会出现汽液两相的流体膜状态,经过模拟分析,流体未发生相变,虽然存在一定的接触力,但整体端面间仍由流体承载为主。
(2)膜厚分布 :从微观膜厚上看,端面间隙的整体趋势为压差增大的微发散型间隙,主要考虑到前期磨损导致 界面形状改变而影响平衡比参数,在发散型间隙的影响 下,端面间的膜压系数会逐渐降低,端面不易开启 [4] ,避 免发生喷漏情况。
4 试验验证
通过模拟现场运行情况(见图 10),对磨损量、磨损 状态、温升3个方面进行试验验证,通过实验现象校核理论计算结果 [5]。
图10 动态试验方案图
4.1 试验关键点
(1) 内侧密封采用特殊设计泵送环,保证流量在15 ~ 20L/min ;(2) 内侧试验件密封采用经过特殊设计的接触式密封,保证运行时仅有极低的温升,避免影响介质侧密封试验结果 ;(3) 机封装配前,用酒精将石墨环彻底擦拭干净,不得有任何石墨粉,避免影响观测结果 ;(4) 隔离液采用与现场密封液理化性质近似的10#工业白油 ; (5) 端面禁止抹油 ;(6) 冲洗液采用水,温度恒定到室温后, 需测水温记录才可进行试验,严格控制冲洗液循环温度及冷却水流量大小 [6]。
4.2 试验结果
4.2.1 连续运转 8h
介质侧 :冲洗管路无温升 ;端面光洁度良好, 动环 无磨损痕迹,静环可见一圈极轻微摩擦痕迹(粗糙度级) (见图 11)。
大气侧 :循环管路温升< 5℃ ; 端面光洁度良好,动 环极轻微摩擦痕迹(粗糙度级),静环内孔可见一圈极轻 微摩擦痕迹(见图 11)。
图11 摩擦副端面
4.2.2 连续运转 12h
介质侧 :冲洗管路无温升 ;端面光洁度良好, 动环无磨损痕迹,静环可见一圈极轻微摩擦痕迹(粗糙度级)(见图 12)。
大气侧 :循环管路温升< 5℃ ; 端面光洁度良好,动环极轻微摩擦痕迹(粗糙度级),静环内孔可见一圈极轻微摩擦痕迹(见图 12)。
图12 摩擦副端面
4.3 试验总结
介质侧 :由水替代轻烃做运转试验,机封几乎在全膜润滑下运行,端面仅有极轻微的摩擦痕迹。将摩擦痕迹放大观察,可看出机封偏内孔接触,主要原因是试验室条件下冲洗水的温度无法达到现场操作温度,同时因流体的动力黏度与导热系数不同,导致试验模拟过程中由温度引起的热锥角超过实际工况数值,使得端面间隙在净锥角偏收敛型时内孔存在接触,其接触承载占比高于流体承载 [7]。
大气侧 :根据用户建议采用理化性质相似的10#工业白油代替耐酸型航空液压油进行模拟实验,试验结果几乎与计算相同。通过收集磨损下的石墨粉可侧面反映端面的接触状态以及流体的承载能力,此密封端面附近几乎无磨损石墨粉残留,通过平镜观察运行稳态后的端面光圈,并未发现端面发生畸变。从平镜观察运转后的动环端面为不到一条氦光带的同心圆,静环端面光带清晰未见磨损,变形及磨损情况符合模拟分析结果。
5 使用反馈
目前用户已使用超过 1 年以上,机封运行平稳,满足用户生产需求。从反馈的拆解照片来看,端面摩擦痕迹均匀,未发生严重磨损,与前期设计结果基本保持一致(见图 13)。
图13 摩擦副端面
6 结语
在特殊工况中为保证机封的使用效果,设计者需格外注意在设计参数满足工况使用条件下,同时需考虑机封与工况环境之间的相互影响。需多方位校核设计参数,如利用有限元分析等,以此得出最优解。特别在操作条件不稳定情况下如何分析混合润滑状态下流体膜承载能力,这关乎整个机封的运行状态。端面的界面形状控制与对流传热之间的关系也需要重点考虑,这在整个运行过程中极为关键。
参考文献
[1] 陈德才,崔德荣.机械密封设计制造与使用[M].北京:机械工业 出版社,1993 .
[2] 顾永泉.机械端面密封主要参数的计算(三):性能参数(续)与计 算示例[J].流体机械,1996,(6):27-32 .
[3] LEBECK A O.Principles and design of mechanical face seals[M].New York:Wiley,1991 .
[4] 顾永泉.机械密封实用技术[M].北京:机械工业出版社,2001 .
[5] 孙开元.机械密封结构图例及应用[M].北京:化学工业出版社, 2017.
[6] 蔡仁良,顾伯勤,宋鹏云.过程装备密封技术[M].北京:化学工业出 版社,2006.
[7] 王汝美.实用机械密封技术问答[M].北京:中国石化出版社,2014.
Design Analysis and Calculation of Seal in Alkylated Sulfuric Acid Reactor
CAO Da,DONG Hui,HU Shenghua,LIU Chenghao
(Dandong Colossus Group Co., Ltd., Dandong Liaoning 118000)
Abstract:Alkylation devices are mainly mature sulfuric acid process, DuPont Stratco process is currently the world'smain representative process for alkylation oil production, Stratco horizontal eccentric reactor is the most mature stirred mixing reactor market share is high, so for the domestic market, reliability of mechanical seal is an important guarantee for its long-term stable operation. In this paper, the key points of seal design of sulfuric acid reactor are analyzed by structural arrangement and theoretical calculation. Mainly from two aspects of the theoretical analysis: 1. Combined with the process, from the heat transfer mechanism to determine the selection scheme; 2. Improve the running state of the machine seal by controlling the shape of the interface between end faces. Reasonable use of the previous successful technical concepts to give the structural parameters, using the finite element software for analysis and verification, input actual working parameters combined with the flow, solid, thermal coupling iteration, calculate the more reliable theoretical results, and finally through the simulation test to verify the reliability of structural parameters.
Key words:alkylation device;mechanical seal of sulfuric acid reactor;heat transfer mechanism;structural parameter